The TRF used on track-type excavator is the key product in Dongyue and is highly concerned by customer. To adapt to the market, ensure rapid response, reduce waste, improve efficiency and accomplish lean management, from Aug. to Dec., Dongyue deployed a process layout optimization project in the production area. Led by Dongyue’s Black Belts with CPS management tool application, to eliminate waste, the project was invested about 15,200 RMB and achieved the expectation.
The project team organized manufacturing, technical and quality personnel in advance to identify the on-site waste and found 15 issues in total:
Ø P(People):2 issues
Ø Q(Quality):2 issues
Ø V(Velocity):5 issues
Ø C(Cost):6 issues
We made improvements according to these 15 issues, here are the improvements and benefits:
Modifying the production line layout to U-shape and changing the single-station to double-station in order to reduce the distance from tacking area to welding area.
It can reduce 300 km/year of turn-round distance and improve 100% space utilization rate.
Integrating CMM into Value Stream, putting the super large hex into production line and making conveyor belt to transfer parts.
It can reduce 400 km/year of transferring distance, save 3000 yuan/year of forklift’s spending and save 508㎡ space occupation from 2528㎡to 2020㎡.
Currently the project has been closed. The company leadership affirmed the achievement meanwhile requested expand the project experience to other area in order to improve the company’s process layout management. At present the related work is in preparation
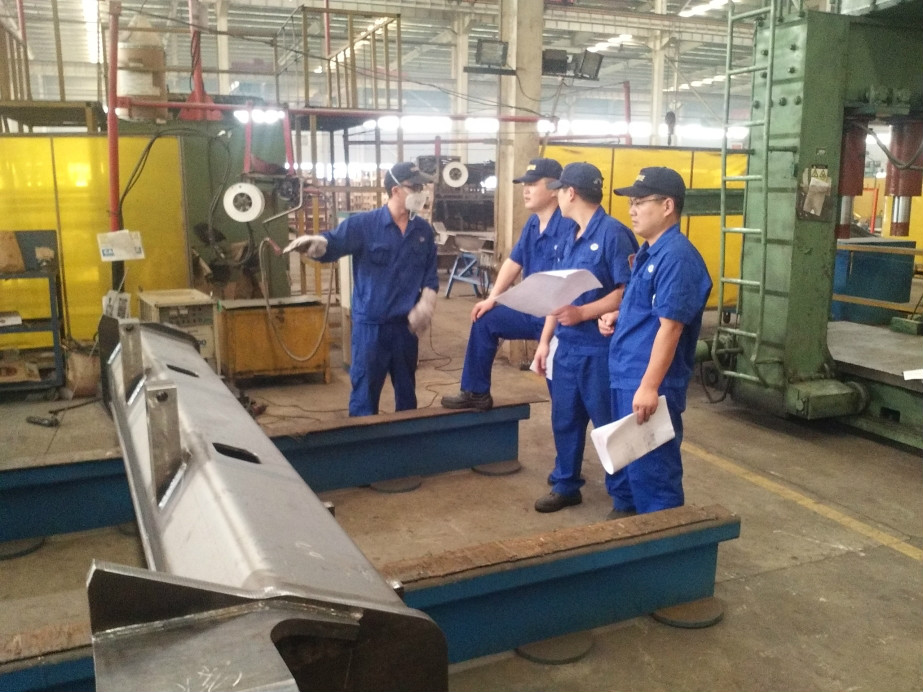
on-site review about process layout by team members
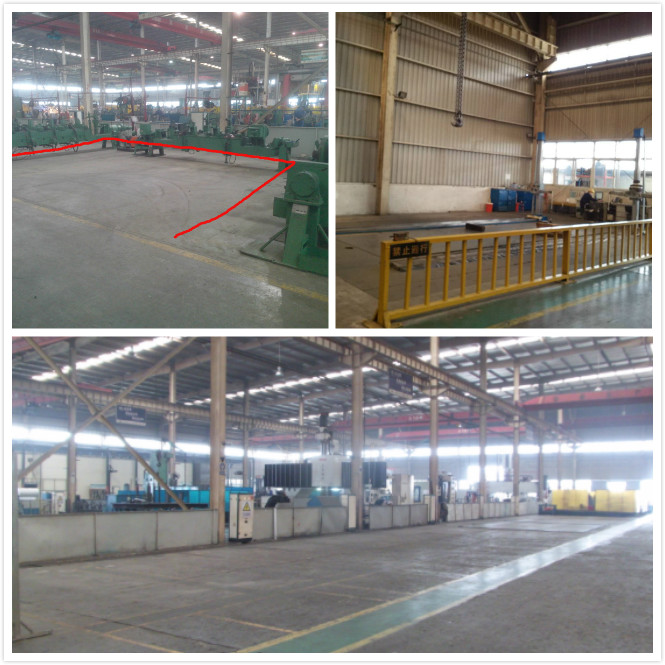
Process layout improvements in workshop